Among
the latest machines in COGIL’s range is a new
type cryogenic freezing spiral that is already set for
further conversion into a mechanical freezing spiral.
This will allow customers to start working with a cryogenic
system, which is commonly known as less costly, smaller,
ten times less demanding in terms of power than mechanical
freezing systems of equal output capacity, until they
have tested out the potential for development of their
new products.
The technical specifications necessary to build this machine
model make this system a little more expensive, initially,
than any conventional cryogenic freezer of equal hourly
output. A very important point is the significant cost
saving feature provided by this system when used as cryogenic
system. Users can save up to 50% on cryogenic gas per
kilogram of product. This reduction on costs is given
by the fact that all the elements of this machine are
designed to facilitate later conversion into a mechanical
system, so the machine comes with a conveyor belt allowing
the product to remain in the refrigerated box during the
freezing procedure.
With the product being allowed to stay in the box for
some time, the temperatures required to perform the freezing
procedure are not more than –35/- 40°C; this
in turn means the ability to use more of the cryogenic
gas enthalpy change.
Another important advantage is that by slightly increasing
the freezing temperature, the user can easily cope with
any peaks in hourly output that may arise from time to
time. A further advantage is that any future conversion
of the cryogenic freezer into a mechanical freezer will
be easily carried out by placing an additional chamber,
with all the parts that are necessary for the transformation
of the unit, next to the cryogenic spiral chamber. The
new chamber will be constructed and thoroughly integrated
at COGIL’s plant.
Technical description of the cryogenic system.
The spiral freezer comprises the following units:
• An insulated enclosure where the freezing process
takes place
• A conveyor belt placed inside the enclosure for
continuous conveyance of products throughout the freezing
cycle
• A ventilation, regulation and cryogen suction
centre
• An automatic conveyor belt washing system
• An electric control panel housing the system’s
centralized controls
The enclosure consists of a one-piece construction with
a stainless sheet steel double wall with 120 mm thick,
self-extinguishing polyurethane foam insulation.
This type of construction, besides providing unlimited
durability, also prevents any water seepage or filtering
of contaminants through the walls hollow spaces. The enclosure
(as shown in the drawing enclosed) is provided with manual
doors allowing full access to all inner parts of the spiral,
making cleaning operations at the end of the work cycle
easy and quick to perform.
The conveyor belt is located inside the enclosure and
moves along a closed circular loop that winds in spiral
around a rotary drum. The length of the freezer belt is
designed according to the hourly output rates expected
from the freezer in its final, mechanical version; therefore,
right from the start, belt length will be threefold the
length that would be necessary for cryogenic freezing
procedures.
The cryogen gas regulation and suction centre consists
of a modulating valve with proportional opening features.
The modulating valve controls the flow of cryogen liquid
into the freezer. Because of the length of the belt, the
required freezing temperature ranges between –30°
and -40°C. A proportional digital thermostat regulates
the temperature. Adequate ventilation is provided all
along the belt circuit to ensure efficient heat exchange
with the freezing product.
Spent gases are sucked in via the product in feed and
out feed openings and are directed to an external exhaust.
The automatic belt washing system is located externally,
in the product loading area and consists of a pipe feeding
a series of spraying nozzles fed by a high-pressure electric
pump.
Washings collect in a tub under the spraying ramp and
then flow into the water drain. The electric panel is
equipped with all the accessories required to assure full
automatic control and operation of the process.
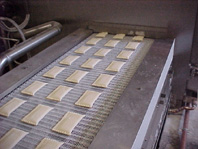
TECHNICAL DESCRIPTION OF THE ACCESSORIES AND REFRIGERATING
CENTRE THAT ARE NECESSARY FOR CONVERTING THE EXISTING
SYSTEM INTO A MECHANICAL FREEZER.
The
cryogenic freezer will be integrated with:
• An insulated enclosure where the refrigeration
accessories are kept
• A mechanical refrigerating centre
• An electric panel for operating the refrigerating
centre
The
enclosure containing the refrigeration accessories (just
like the freezing enclosure) consists of a one-piece construction
with a stainless sheet steel double wall with 120 mm thick,
self-extinguishing polyurethane foam insulation.
As shown in the drawing enclosed, the enclosure is provided
with manual doors allowing full access to all inner parts
of the spiral, making cleaning operations at the end of
the work cycle easy and quick to perform.
Full access to all evaporator parts is also provided.
Inside the enclosure is a conduit of stainless steel panels
to assure even delivery of cold air on and around the
product at a speed of approx. 3 metres per second.
The refrigeration unit for mechanical product freezing
is based on screw compressors with separate circuits for
independent operation, to be positioned externally and
away from the unit.
The air cooling evaporator consists of a battery with
copper tubes and copper fins, designed to expand FREON
gas directly. The battery has a double stage construction
so the air can be cooled to –40°C when freezing
at full speed.
The air circuit, which assures heat exchange with the
battery as well as product ventilation during the freezing
process, is provided with centrifugal electric fans with
the fan wheels positioned inside the enclosure and the
motors positioned on the outside.
|